在現代工業和科研領域,低溫試驗機的測試效率對于產品研發和質量控制至關重要。傳統設備的制冷效率往往受限于技術瓶頸,導致測試周期較長。然而,隨著智能制冷系統的引入,這一問題得到了顯著改善。通過技術手段,設備的測試產能得以大幅提升,甚至可實現40%以上的效率提升。
1. 自適應變頻制冷技術:按需供冷,極速降溫
傳統設備采用定頻壓縮機,制冷量固定,降溫過程中常因“過冷”或“不足”導致效率低下。智能系統搭載變頻壓縮機與AI算法,實時感知低溫試驗機內溫度與目標值的偏差,動態調節制冷功率。例如,從常溫降至-40℃時,系統前3分鐘以很大功率快速降溫,隨后自動切換至低頻維持,避免過度制冷。某電子元件測試中,降溫階段從45分鐘縮短至25分鐘,單次測試效率提升44%。
2. 多級熱交換優化:打破溫度恢復瓶頸 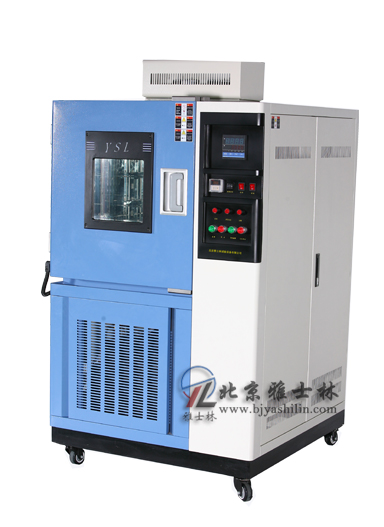
傳統低溫試驗機在測試結束后需長時間自然回溫,導致連續測試產能低。智能系統采用雙級熱交換+余熱回收技術,在降溫階段通過冷凝器預存熱量,測試結束后利用回收余熱加速升溫。例如,從-60℃回升至室溫僅需20分鐘,較傳統設備的2小時縮短83%。某新能源電池企業因此實現每日測試批次從8次增至12次,產能提升50%。
3. 預測性維護算法:減少停機,保障持續高效
傳統設備因缺乏預警機制,常因故障導致停機,影響整體效率。智能系統內置機器學習模型,通過分析壓縮機振動、壓力傳感器數據等,提前72小時預測潛在故障(如制冷劑泄漏、冷凝器結霜)。某汽車零部件廠商應用后,設備年非計劃停機時間從15天降至3天,綜合測試產能提升28%。
智能制冷系統的引入為低溫試驗機帶來了革命性的變化。
|